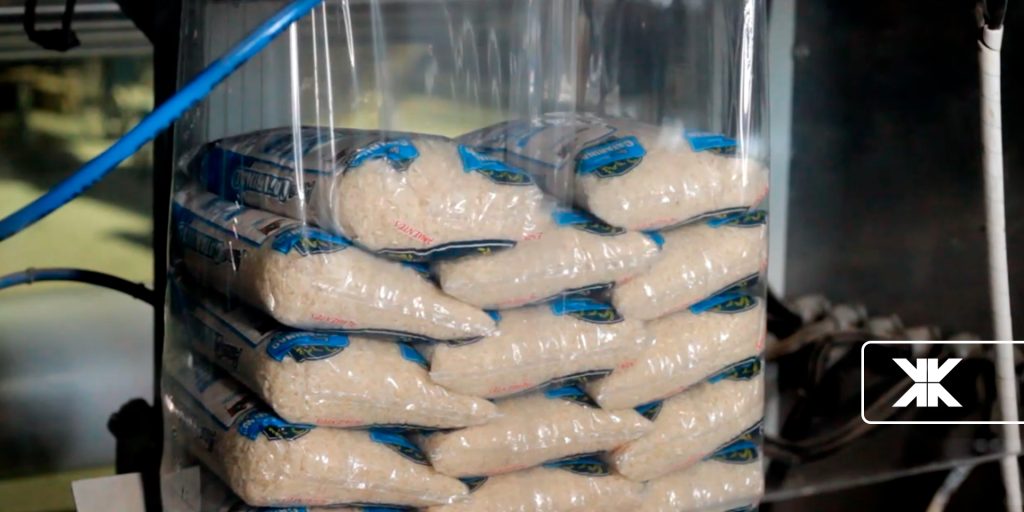
Categoria: Grouping, Maintenance and Operation, Processes
5 challenges of automatic baling and how to solve them
Automatic baling is an essential step in the production and packaging chain, providing efficiency and consistency in the secondary packaging of products.
However, this process can bring some challenges that can impact baling quality and operational efficiency.
Below, we’ll explore 5 challenges in automatic baling, possible causes, and how to practically resolve them to maintain your productivity.
Good reading!
Challenges of automatic baling
Addressing the challenges associated with this process can significantly improve the efficiency and quality of packaged products.
Identifying and solving problems such as packages falling into the bale, sealing quality or equipment repairs and maintenance, for example, is essential to optimizing the baling process.
Discover the 5 main challenges in automatic baling and learn how to solve them:
1. Packages falling into the bale
One of the common challenges in automatic baling is the packages falling when the bale is formed. This problem can harm the integrity of the packaging, in addition to compromising the efficiency of the process as a whole.
Possible causes:
- Variable package density: products with different densities can behave unpredictably during stacking, resulting in disorganized bales;
- Improvised manual adjustments: changes made manually to the package drop configuration can result in disorderly stacks, affecting the final quality of the bale.
How to solve:
- Proper adjustment: ensure that the package drop configuration is calibrated according to the continuous flow of packages coming from the packaging machines, maintaining the direction and shape;
- Monitoring and adjustments: carry out periodic checks on package densities and adjust the system to compensate for possible variations, avoiding stacking disorder.
2. Sealing quality
Another challenge in automatic baling is ensuring sealing quality. This becomes more complex due to component wear and possible inadequacy of the plastic film. Inadequate sealing can compromise the integrity of the bale during transportation and storage, resulting in product losses and rework.
Possible causes:
- Wear of sealing components: Sealing metal and other consumable components can wear out over time due to constant heat;
- Inadequate film thickness: plastic film may not be strong enough to withstand transportation.
How to solve:
- Component check and replacement: regularly inspect and replace solder consumable elements (resistance, silicone and Teflon). Use appropriate tools and assemble the components according to specifications;
- Film thickness analysis: ensure that the plastic film thickness is adequate to withstand impact forces during transportation.
Read also: Sustainable baling: How to reduce environmental impact
3. System of interconnection of two or three packaging machines
Maintaining a continuous and efficient flow in automatic baling is essential to guarantee productivity and quality. However, manual interference and inappropriate changes to the system can cause imbalances in the process.
Possible causes:
- Inadequate changes to the interface: changes in system parameters or production speeds can destabilize operation;
- Manual interference: Placing packages manually while packaging machines are in operation can cause problems in the production flow.
How to solve:
- Proper parameter management: keep parameters and production speeds consistent and avoid changes without adequate planning;
- Avoid interference: Do not place packages manually during automatic operation. Trust the system to keep you flowing and in sync.
4. Disregarding manufacturer guidelines for repairs and maintenance
Proper maintenance and repairs are crucial to ensuring the proper functioning of baling equipment. Ignoring the manufacturer’s recommendations can compromise the system’s efficiency and useful life.
Possible causes:
- Inadequate maintenance: repairs and replacements not carried out according to the manufacturer’s specifications can lead to failures;
- Use of inferior components: replacing parts with inferior quality components may compromise equipment performance.
How to solve:
- Follow the manufacturer’s recommendations: carry out repairs and replace components according to the manufacturer’s guidelines to ensure proper functioning of the equipment;
- Preventative maintenance: Establish a regular maintenance schedule to ensure all parts of the equipment are in good working order.
5. Lack of regular equipment cleaning
Regular equipment maintenance is crucial to ensuring the efficiency and durability of your automatic baling system. Lack of adequate cleaning can lead to serious problems that affect the performance and quality of the baling process. Let’s explore the main causes of this problem and solutions to prevent it.
Possible causes:
- Accumulation of dust: dust from the product can accumulate on the equipment, causing wear, due to the abrasive effect;
- Dirt and impurities from the environment: dust raised from the floor comes into contact with the equipment and plastic film, contributing to accumulated dirt and possible damage.
How to solve:
- Cleaning routine: implement a periodic and detailed cleaning schedule to remove dirt and impurities, ensuring that all parts of the equipment, including belts and areas in contact with the plastic film, are cleaned regularly;
- Dust control: adopt measures to reduce dust in the environment, such as using adequate ventilation systems and keeping the floor clean. This will help minimize dust buildup on the equipment and plastic wrap.
Read also: 4 actions to optimize the layout of your industry’s packaging line
With proper adjustments, selection of high-quality materials and continuous staff training, it is possible to overcome these challenges and ensure an efficient baling process.
In addition to the practical solutions mentioned, qualified technical assistance is a great ally to guarantee the ideal performance of the equipment.
Our experience shows that with technical support and preventative maintenance, it is possible to avoid problems and ensure that the baling system operates at maximum efficiency.
Count on Indumak after-sales service to support your operation in all your possible needs, with Technical Assistance and Personalized Support.