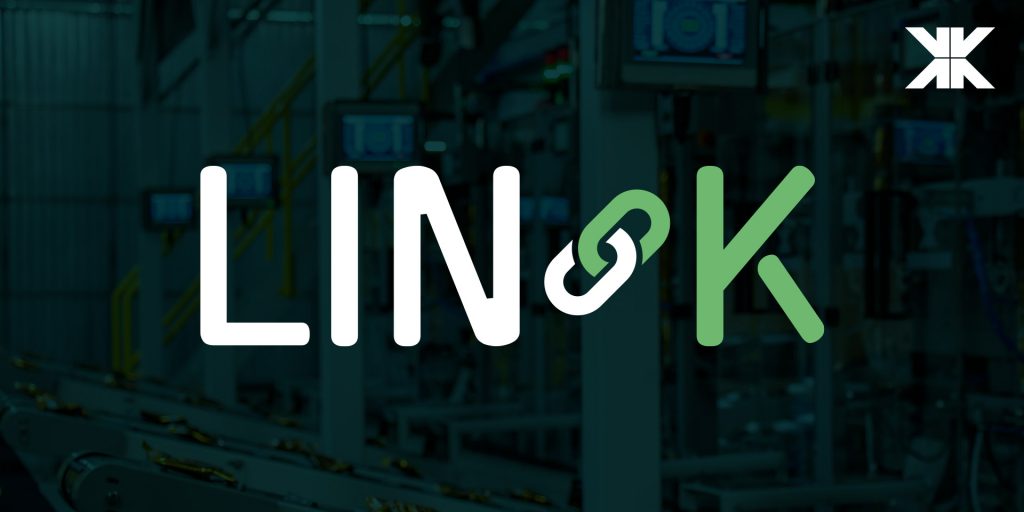
Categoria: Innovation
GET TO KNOW LIN-K, THE INDUMAK EQUIPMENT REMOTE MONITORING PROGRAM
You certainly enjoy reading about the future of the industry, about technology and improvements in the efficiency and productivity of the processes involved, and about market trends.
Digital transformation has made it possible for us to have information and data in the palm of our hand in order to find answers and achieve business goals.
We know that advanced technologies can help in the evolution and growth of the industry and we are concerned with helping and carrying out actions for the effectiveness of these programs and these tools.
Therefore, focused on increasing the competitiveness and productivity of client companies, Indumak, through Industry 4.0 innovations, developed a project that seeks to identify information and evaluate the results obtained with the automation of packaging: it is LIN-K, the Indumak equipment remote monitoring program.
What will LIN-K be able to do?
With the program, it is possible to analyze industrial performance data and visualize the changes that must be made to improve results.
Thus, guidelines and plans are created for what needs to be done so that it is possible to extract the best from the equipment, allowing new studies to understand the next steps. It is the practical application of the concept of continuous improvement.
How will the LIN-K remote monitoring program work?
With a cloud-based platform, Indumak is developing an interface that makes it possible to view the machine’s productive data from any device connected to the Internet through a browser, similar to accessing a website.
All access is protected by a unique username and password, in addition to all the digital security of data storage.
Instrumentation and measurement
In order to avoid major changes and enable implementation in equipment already in operation, the devices already present in them will initially be used, without the need to change the automation.
Control
At this moment, no change in the control of the machines will be implemented, that is, all the parameterization is maintained as it is currently performed. The PLC maintains the same interface, and the parameters already configured will also remain the same. No additional training will be required for machine operators.
Infrastructure
By using cloud storage, data persistence and backup are guaranteed by a company specializing in this type of technology, as well as the possibility of automatically expanding storage capacity (scalability), allowing all generated data to be stored indefinitely.
For this, an efficient internet connection is required. No data will be stored locally.
For this communication to occur, in addition to the availability of an internet point close to the machine, it is necessary to install an edge device (gateway) that will send the data collected by the machines.
Operation
The operation remains exclusively local, and it is not possible to operate remotely, aiming at safety. However, the visualization of all data generated in production can be performed from any device with internet access through the browser.
The gains and advantages of remote equipment monitoring
Benefits include reduced unscheduled downtime and maximum use of machinery capacity. See more below.
Support for decision making
-
Maintenance
A long history of failure and alarm occurrences makes it possible to identify preventive and predictive maintenance needs.
If requested, Indumak’s support team can carry out an analysis of the failure history, facilitating the identification of problems and their respective causes in a faster and more assertive way.
For more in-depth support, Indumak’s support team can perform remote access to the equipment (PLC and HMI) for monitoring and/or software updates.
-
Production Management
With the machine status history, it is possible to visualize in graphic form the times of the machine stopped or in production, as well as to follow the production in intervals defined by the manager according to the need of the query.
Based on these data, indicators will be calculated by the system, generating more information that will help in decision making.
During the implementation and the perception of needs, new information can be implemented in the system.
Sorting the data generated by equipment in the packaging industry allows you to measure success and identify the way forward.