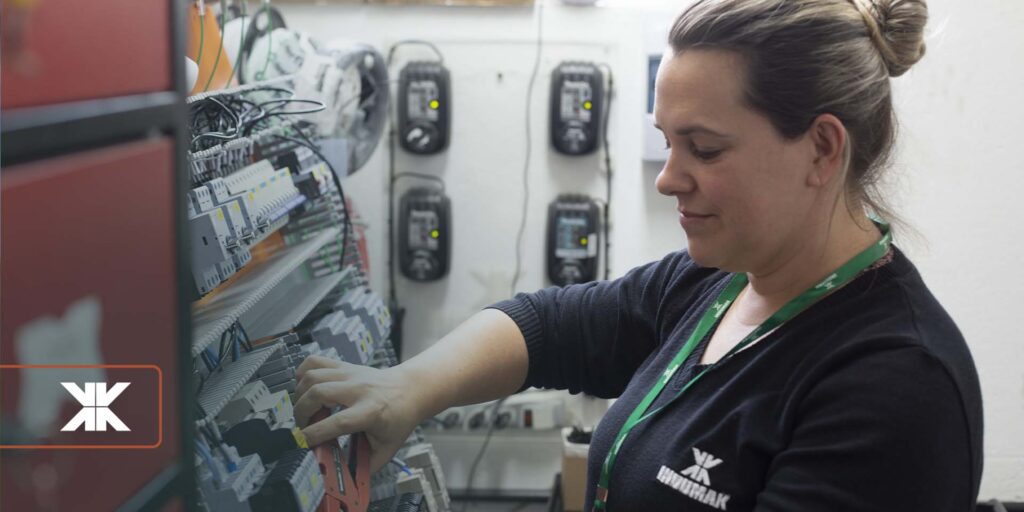
Categoria: Packaging, Processes
HOW TO AVOID BOTTLENECKS IN THE FOOD INDUSTRY IN THE PACKAGING PROCESS
In industry, the term “bottleneck” is used to refer to a point in the production process that limits the company’s ability to produce in greater quantity and with greater efficiency.
This is where production “hangs” requiring more time for a certain step or steps to be completed.
Bottlenecks in the food industry can arise in various phases, such as in the production, storage and distribution of food. However, one of the most common blockages occurs in the packaging process.
Check out the following content for tips on how to avoid this in your industry.
Tips to avoid bottlenecks in your food industry
Below, we list some actions that can be put in place to prevent this from happening, ensuring fluidity for your factory.
1. Analyze your production processes
The first step is to identify the critical points that exist in your production process.
Make a detailed analysis of the entire path that the raw material travels until it becomes the final commodity. It may be responsible for a bottleneck in non-receipt, delay in delivery, waste or non-compliance.
Check where there is greater accumulation of tasks and/or longer processing time. This can help you identify bottlenecks and plan more efficient solutions to deal with them.
The supply and feeding for the packaging sector are some of the steps that precede the entire packaging part of the product in the industry. The control of them are crucial so that the others are met with the time and the existing resource.
2. Invest in quality equipment
Packaging is crucial in the food industry as it is responsible for ensuring product quality and safety, as well as directly influencing consumer satisfaction. Because the lack of investment in quality machinery and equipment can compromise the efficiency and productivity of the company.
One of the main bottlenecks in the packaging process is precisely the low production speed or unscheduled stops. This can happen when the machines used are not able to keep up with the company’s production pace or when frequent shutdowns occur for maintenance and adjustments.
To avoid this problem, it is important to invest in high-performance machinery and equipment, capable of processing large amounts of food in less time and with minimal need for maintenance. And also control the stock of parts that suffer natural wear, as well as preventive maintenance.
Read also: How to make the rice packaging process more agile.
3. Bet on automation to improve processes
Another common bottleneck in the packaging process is the lack of automation.
When the process is done manually, the production time is much longer, which can lead to delays in product delivery.
In addition, manual operations increase the risk of errors and failures, can affect the quality of the product handled, weight, welds, safety, among others.
Again, investing in automated machinery and equipment can help improve process efficiency, reduce errors, and ensure product quality.
With automation, the analysis of real productive data is also facilitated by delivering a macro view of the productive health of the sector.
Read also: 6 advantages of automatic palletizing that you need to know.
4. Train your team often
Prepare your employees to be more efficient and productive in their tasks.
This can involve everything from identifying more efficient working techniques to taking a more collaborative approach to dealing with problems and reducing downtime.
Based on the first points highlighted in this text, an alert related to labor can be evidenced as a root cause. The training of operators is essential for a production process that meets all the manufacturing demand, with good results.
5. Increase your production capacity
Finally, consider increasing your plant’s capacity, as it may no longer support market demand for your products.
This means planning from the physical expansion of the industrial park to the adoption of new equipment and technologies that allow to increase production without compromising the quality or efficiency of the process.
It is important to remember that effectively reducing bottlenecks in the food industry requires strategic planning and long-term investments.
The adoption of advanced technologies, the optimization of production processes and the continuous improvement of the team are some of the factors that contribute to the reduction of bottlenecks and to the increase of the efficiency and competitiveness of the company.