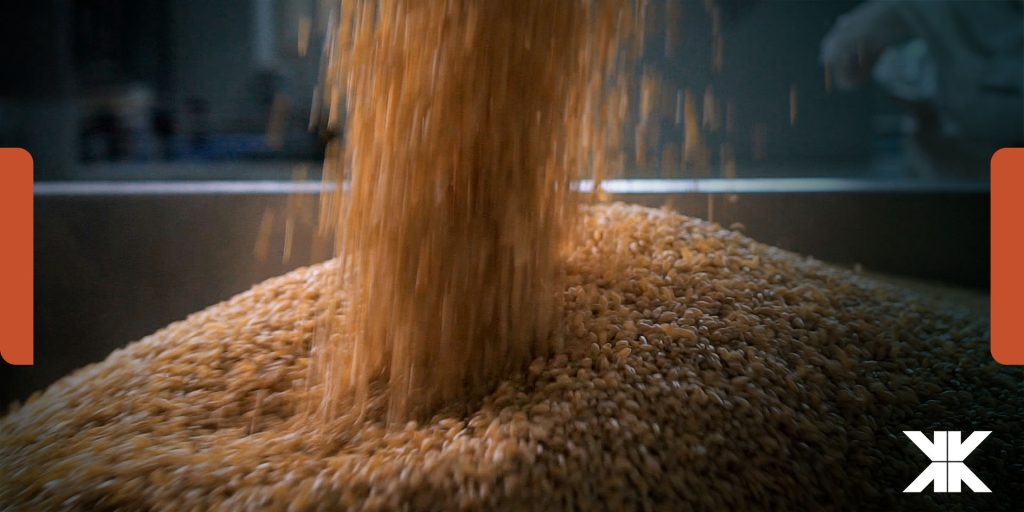
Categoria: Packaging
PACKAGING CEREALS: HOW TO OPTIMIZE THIS PROCESS
Cereal packaging is an important process to ensure product protection against contamination and damage during transport.
First, it is always good to remember that food handling by a cereal packaging company must follow a set of strict principles and rules that will guarantee the quality and safety demanded by consumers.
For this reason, it is essential to invest in an infrastructure that meets the legislation and allows the processing of cereals to be done, ensuring a high quality standard, avoiding contamination and other problems that could compromise the properties of the food.
It is precisely in the cereal packaging stage that vulnerabilities can occur.
See some of the problems that can happen in the packaging process:
- Contamination by foreign bodies;
- Weighing errors;
- Badly closed or perforated packages;
- Slowness due to bottlenecks;
- Unscheduled equipment shutdowns.
Now that you know what can go wrong, let’s show 4 tips to optimize the cereal packaging process.
4 tips for optimizing cereal packaging
1 – Invest in high-performance automatic packing machines
Currently, there are several models of automatic packaging machines to carry out the packaging of cereals that bring gains such as the standardization of packages, the reduction of risks of contamination and the risk of accidents with employees.
There are economic models that surprise with their high performance.
If your goal is to scale your business and increase your production capacity, purchasing a high-performance automatic packaging machine is an excellent option to make your company’s packaging process even more agile.
Invest in automatic packing machines from reliable and helpful suppliers, such as Indumak, which has close customer service and an ever-present after-sales service. Discover Indumak’s automatic packaging lines here.
2 – Adopt the use of fillers, checkweigher and metal detector
One of the regulatory requirements of consumer rights is the weight of packages, which must always correspond to the information disclosed on the labels.
To meet this requirement, the use of filelrs becomes indispensable. But, after the product is packaged, it is necessary to check that the weight of the package is correct.
For this, the checkweigher, a device used to check the weight of the package, becomes essential to check the weight quickly and accurately. If any package is not within the indicated weight range, it is identified and removed automatically using this device. Learn more about checkweigher here.
Another accessory that offers benefits for cereal packaging is the metal detector responsible for detecting and expelling foreign bodies during the process. Learn more about the metal detector here.
Indumak’s metal detector is a safe, efficient piece of equipment, with the expertise of the Brazilian leader in automatic packaging, designed to be connected to the packaging machine and guarantee safer and more impeccable packages.
3 – Perform load unitization with a high-performance baler
Unitizing a load means grouping small or large packages into a single standardized volume in order to facilitate its handling, movement, storage and transport.
The adoption of this procedure facilitates the logistical work, in addition to bringing more efficiency and reducing costs in the storage and distribution sector, with advantages that include:
- Reduction in the number of volumes that must be handled, promoting time savings;
- Better use of useful space;
- Decrease in the number of cargo handlings and use of less labor;
- Possibility of mechanizing loading and unloading operations;
- Reduction of time and costs of boarding and disembarking;
- Reduction of packaging costs;
- Decrease in breakdowns and theft of goods, as they are safer when grouped together;
- Reduction of goods insurance costs. You are probably already aware of the benefits of unitizing loads mentioned above. But do you know that load unitization can be done faster?
Indumak offers in its portfolio the MK 30, the fastest baler in the world and well regarded in the market. Its flexibility and high performance guarantee more productive efficiency and operational gains. Know the solution.
4 – Plan preventive maintenance
Unscheduled downtime due to equipment breakdowns are the main cause of productivity declines in a business.
Not to mention the damage that is usually greater when a machine suddenly breaks down due to lack of maintenance.
Therefore, this last recommendation could not be different: take care of your company’s assets and do not ignore the need to have – and put into practice – a regular preventive maintenance plan.
With a maintenance plan, you can avoid unscheduled downtime, prevent work accidents and the degradation of your machines.
Learn more about Indumak
Indumak is a pioneer and market leader in solutions for packaging, bagging, grouping and moving goods, including cereal packaging.
Our lines are specially developed to offer the maximum level of efficiency for the final manufacturing stages, meeting the demand of Brazilian and world industries in different segments: food, civil construction, animal feed, among others.
All of our solutions can be integrated, working harmoniously to offer the security, savings and productivity that your business deserves. To talk to an Indumak expert consultant, request a contact here.