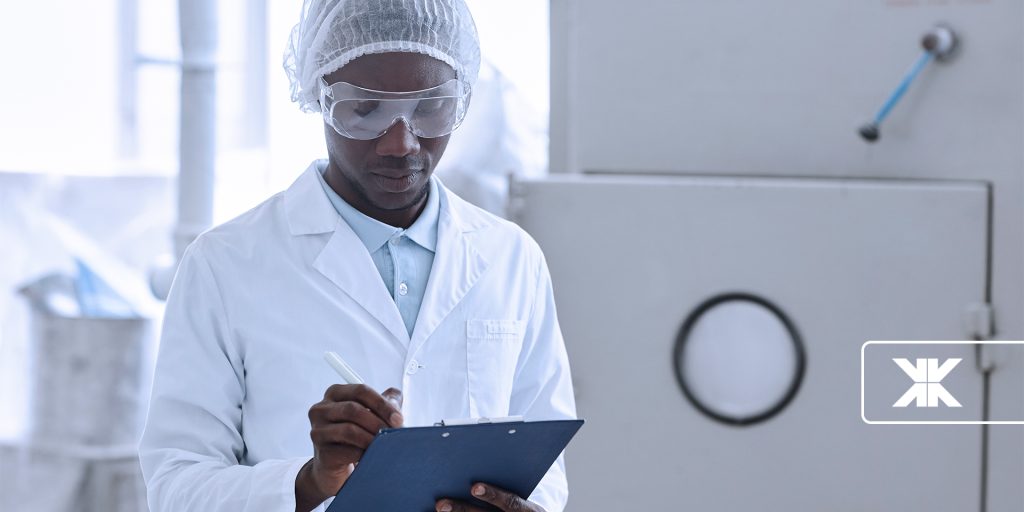
Categoria: Management, Processes
PRODUCTION GUIDELINES: BEST PRACTICES TO INCREASE INDUSTRIAL EFFICIENCY
Do you know the importance of production guidelines for an efficient manufacturing line?
Production guidelines help to define the steps that must be taken at each stage of the manufacturing line, aiming for greater integration between processes and guiding employees to carry out their activities based on pre-agreed rules and guidelines.
These guidelines not only increase efficiency, but also reduce errors and improve the quality of the final product.
In this content, we’ll explore best practices for implementing effective production guidelines and how they can transform your industrial operation. Continue reading to find out more.
Benefits of following well-defined production guidelines
Companies that have well-defined production guidelines that are strictly followed often have better performance metrics in various sectors, since when there is a clear and pre-determined guideline, all employees work towards the same objective. Among the objectives, it is possible to observe:
- Increased efficiency: standardized processes reduce production time and avoid rework.
- Consistent quality: Clear guidelines ensure that all products meet the same quality standards.
- Reduction of errors: detailed guidelines minimize the occurrence of errors and deviations in the production process.
- Improved safety: Standardized procedures promote a safer work environment.
- Facilitated training: new employees are trained faster and more effectively.
These benefits help optimize production and achieve better operational results.
Read also: How to apply continuous improvement in packaging?
Points of attention to implement production guidelines effectively
Implementing well-defined production guidelines is essential to increasing industrial efficiency. This involves a thorough analysis of existing processes, clear definition of objectives, detailed mapping of production steps and the creation of specific action plans.
Effective communication and appropriate resource allocation are also key. Continue reading to understand the main points of attention for the successful implementation and continuous improvement of production processes.
Analysis and planning
Carry out a detailed analysis of existing processes on the production line. Identify bottlenecks, inefficiencies and areas in need of improvement. Engage all stakeholders, from operators to managers, to gain a complete, comprehensive view.
Establish clear and measurable goals for implementing production guidelines. These objectives must align with the company’s strategic vision and focus on improving efficiency, quality and safety.
From there, develop specific action plans to address the identified areas of improvement. These plans must include necessary resources, schedules and people responsible for each task.
Clear documentation
Clear documentation is a key component to effectively implementing production guidelines. It must include detailed descriptions of each step of the process, employee responsibilities, quality standards and operational procedures.
Clarity in documentation helps avoid ambiguities, ensuring that everyone involved fully understands their roles and expectations. In addition, it facilitates the training of new employees and serves as a continuous reference for problem solving and process improvements.
Continuous training
To ensure that all employees understand and follow production guidelines, provide well-structured ongoing training. Start with needs analysis and develop clear educational materials.
Use varied methodologies, such as in-person and online training and practical simulations. Ensure qualified instructors conduct training and assess employee knowledge through testing and feedback.
Update content regularly and keep detailed records to monitor progress and adjust training as needed.
Monitoring and evaluation
To monitor and evaluate adherence to guidelines, implement systems that track employee performance and compliance with established practices. Use monitoring tools such as performance reports and regular audits.
Conduct periodic evaluations to measure the effectiveness of the guidelines by analyzing data and collecting feedback. Identify areas for improvement and adjust practices as needed. This process ensures that guidelines are followed correctly and promotes continuous process improvement.
Feedback and adjustments
To improve processes, regularly collect feedback from employees on the application of the guidelines. Use surveys, meetings, and performance reviews to gain in-depth information. Analyze feedback to identify problems and areas for improvement.
Based on this information, make adjustments to guidelines and procedures to correct errors and optimize processes. This cycle of continuous feedback and adjustments helps keep the guidelines effective and adapted to the real needs of the workplace.
Use of technologies
To optimize processes, use technologies that automate and standardize tasks. Implementing management and automation software can reduce errors and increase efficiency when performing repetitive and complex tasks.
Tools like ERP systems, monitoring apps, and communication platforms help maintain accuracy and consistency. The integration of technologies also facilitates process monitoring and data analysis, allowing for quick and informed adjustments, thus improving efficiency and overall quality.
Using technologies to automate and standardize manufacturing processes and tasks, such as packaging, brings many benefits. Automated systems can package products quickly and accurately, reducing errors and increasing efficiency.
Implementing automated packaging machines minimizes manual labor and ensures consistency in packaging quality. These technologies also facilitate tracking and integration with other management systems, enabling a more efficient workflow and data collection for continuous analysis and adjustments.
Read also: Understand how industrial automation improves employee well-being
Optimization of production processes
In addition to automation, there are continuous improvement methods that help any project management become more efficient. Among them are, for example:
Kaizen – change for the better
Japanese method based on 5 principles that believes that everything can be improved through small adjustments that turn into big changes: Sense of use, Sense of organization, Sense of cleanliness, Sense of health and hygiene, Sense of self-discipline.
Each of the senses can be implemented on different fronts and in any sector, and leads to a process of continuous improvement that does not necessarily have to end, seeking increasingly higher levels of efficiency and quality.
Lean manufacturing
Lean manufacturing is an approach focused on maximizing customer value while minimizing waste and increasing efficiency. When applied to the optimization of production processes, especially in the context of the Internet of Things (IoT), lean manufacturing can offer great benefits.
Quality management
To ensure the quality of the final product, implement quality management guidelines that include rigorous inspections and standardized procedures.
Establish clear quality criteria and use control tools, such as control charts and statistical analysis, to monitor performance. Perform periodic audits and provide ongoing training for employees.
Document and analyze non-conformities to implement corrective and preventive actions.
All of these actions favor not only the organization and operational management of projects, but also the strategic planning of the company as a whole, through informed data analysis and more assertive decision-making.
If you want to implement production guidelines in your manufacturing plants, count on the expertise of Indumak, which has been helping the industry to ensure a more automated and optimized structure for more than 60 years, for greater productivity and competitiveness.