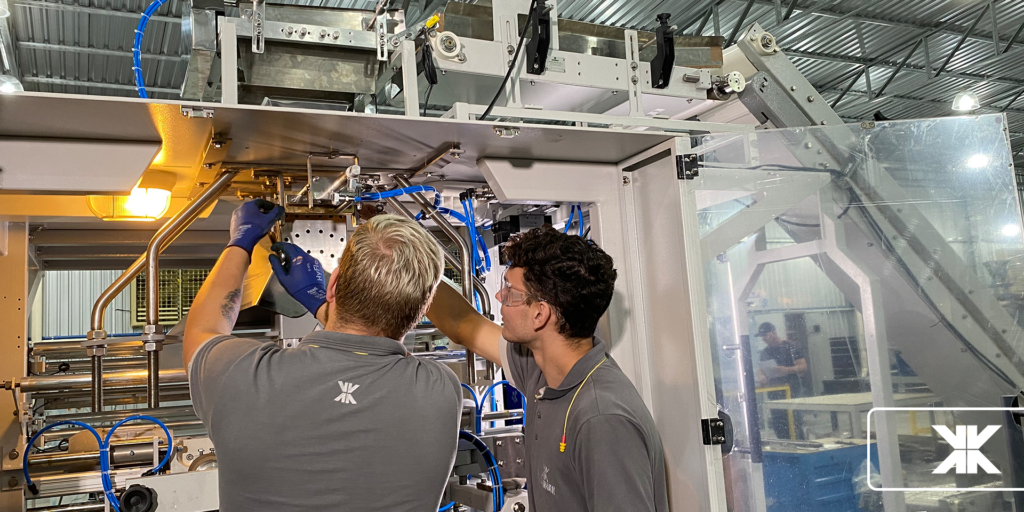
Categoria: Management
THE IMPORTANCE OF EMPLOYEE TRAINING IN THE AUTOMATIC PACKAGING PROCESS
The automation of processes in industry is, with no doubt, a major advance. Suddenly, we were able to save time, save resources and increase profits with increasingly efficient machinery.
However, human action was still necessary. Quite the opposite! Now, in addition to being indispensable, it also needs to be highly qualified. Therefore, the operational training of employees in the packaging process is essential.
So, we have prepared content to help you understand more about this issue. Continue reading to understand the importance of training these professionals and check out tips to make this possible.
What is operational capability?
Training employees in the packaging process is a set of actions and training designed to prepare employees who work in the segment, in order to train them to perform their functions efficiently, safely and productively.
This training can be carried out both for new employees who are being incorporated into the team and for existing employees who need to update their knowledge and skills.
Why is operational training essential when handling machines?
Training employees is essential for several essential reasons for the smooth functioning and safety of operations. See below for reasons why this training cannot be left out of your automation planning.
Read also: Understand how industrial automation improves employee well-being
Employee safety
Improper handling of machines can pose significant risks to employee safety. The training teaches correct operating practices and use of protective equipment (PPE), reducing the risk of accidents and injuries.
Preventing damage to equipment
Ignorance or incorrect use of machines can result in damage to equipment, which can be costly for the company and cause numerous losses.
Therefore, training helps ensure that employees know how to use machines correctly, prolonging their useful life.
Operational efficiency
Qualified employees are more proficient in handling machines, which leads to greater efficiency in operations and, consequently, an increase in productivity and less downtime for machinery and production in general.
Quality of work
Adequate training ensures that employees know how to operate machines accurately and consistently, contributing to the quality of the work performed.
This is especially important in processes such as packaging, where precision is essential to ensure compliance with quality standards and customer satisfaction.
Reduction of errors and waste
Trained employees are less likely to make mistakes when handling machines. This helps reduce material waste and avoids the need for rework, which positively impacts production costs.
Adapting to new technologies
With rapid technological evolution, machines and equipment are always being updated. Continuous training allows employees to adapt more easily to new technologies and innovations.
Keeping the company competitive in the market and reducing the need to hire new employees, which can be costly and not interesting for business.
Furthermore, it is essential that companies invest in infrastructure and technology to improve service provision, reduce water losses, improve sewage collection and treatment, and optimize solid waste management.
Compliance with rules and regulations
Finally, another advantage is the company’s compliance with the rules and safety regulations related to the handling of machines. This is essential to avoid penalties and ensure the safety of everyone involved. Now, check out some tips to make this training possible and really efficient.
How to take of operators trainning in the packaging process
Check some tips to make this trainning workable and efficient.
Identify training needs
Before starting training, identify what skills and knowledge are needed for the packaging process. This can be checked with the manufacturers themselves or through specific Occupational Safety consultancies.
Consider the different types of products to be packaged, the equipment used and the relevant safety procedures. And do what you can to implement the best ways of learning.
Develop a training program
Based on the identified needs, create a detailed training program. Determine the topics to be covered, the duration of the training, the resources needed and the teaching methods that will be used.
Combine theoretical training with practical training to provide a complete learning experience. Employees must understand both the theory and practical application knowledge in the packaging process.
Include safety training
Don’t just stick to theory! We have already mentioned the importance of practice in this entire context, but it cannot be stressed enough that it is important to focus on safety throughout the process.
Give special emphasis to safety training, emphasizing the importance of proper use of personal protective equipment (PPE) and safety procedures to avoid accidents.
Conduct group and individual training
Organize group trainings to cover general topics and common aspects of the packaging process. Additionally, provide individual training to address each employee’s specific needs.
Be sure to encourage active participation from employees during training.
Allow them to ask questions, share their experiences and suggest improvements.
Conduct performance reviews
After training, evaluate employees’ performance to ensure they have acquired the necessary skills. This can be done through tests, simulations and practical assessments.
And don’t forget to encourage employees to provide feedback on training and day-to-day work. Use this information to continually improve your training program, as updates never stop coming.
As we can see, training employees in the packaging process is essential. It helps prevent accidents and makes your business flow more efficiently and naturally.