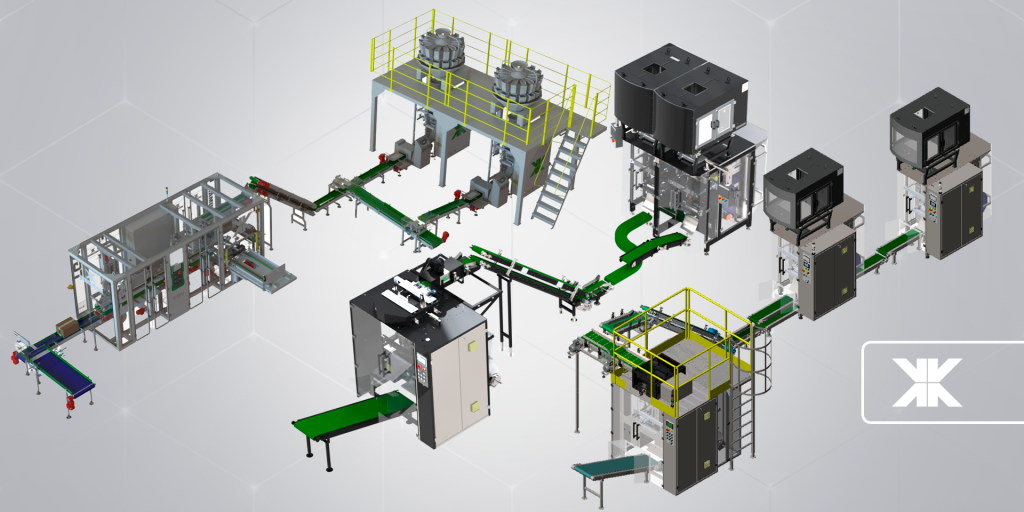
Categoria: Maintenance and Operation
DISCOVER THE INTERCONNECTIONS OF INDUMAK MACHINES: GUARANTEE OF INCREASED PRODUCTIVITY
The packaging industry is a vital force in several industrial sectors, being crucial in the protection, presentation and distribution of products to end consumers.
In a highly competitive market, packaging efficiency plays a key role in a company’s ability to meet market demands and remain profitable.
In this context, Indumak equipment plays a central role. The way the machines are interconnected – packaging machines with the grouping stage – directly influences the efficiency and quality of the baled or boxed products.
Continue reading to learn about the interconnection models that Indumak machines incorporate into their projects, providing customers with a guaranteed increase in productivity.
Indumak machine interconnection models
To achieve maximum efficiency in the operation of packaging, baling or boxing machines, it is essential to understand the different forms of interconnection available.
Below, we will present the interconnection models, highlighting their main advantages and essential points of attention to be considered before investing in an interconnected system.
Read also: How to start integrating production lines to achieve more productivity and profitability
Model L: two packaging machines for one baler with package tipping or flap
Model L is the most common integration model, as it originated with the migration from manual to automatic baling, the installation of balers, using the customer’s existing installations and machine layouts.
Its implementation involves joining packages from two packaging machines onto a single belt that feeds the baler.
During this line integration process, packages from the main machine – which is directly aligned with the baler – are directed to the baler with adequate spacing, allowing the interconnection of packages from the secondary machine.
The secondary machine packages, in turn, are subjected to two tumbles to transfer the direction of movement. This movement can occur through direct falling or through flaps, especially in packages that are more sensitive to free tipping.
Advantages of Model L
Check out the advantages that the Model L offers below:
- Quick installation: this alternative for interconnecting Indumak machines uses the current positions of the packaging machines on the customer’s premises, meaning there is no need to reposition them or their feeds, facilitating the baler installation process.
- Operation of packaging machines: it is common for the same operator to supervise both machines, therefore the adoption of Model L reduces the need for extensive travel by professionals, making the process practical and efficient.
One suggestion is to choose (when possible) to order packaging machines with inverted panel sides. In this case, the two panels are towards the center of the machines.
Points of attention of the Model L
We highlight two points of attention for this model:
- Choice between tipping and flap: there are packages that do not behave well with free tipping and require the use of flaps. This definition needs to take into account the characteristics of the product and the dynamics of the packages to be assertive
- Alerts regarding packaging: attention must be paid to packaging with sliders and the positioning of packages on the conveyor belt to ensure greater precision. Too much sliding in the packaging can hinder the tipping and correct alignment of the packages, which impairs the positioning of the bale.
Model S: two packaging machines and a baler with curved plastic belt insert
The Model S appears as a strategic choice when seeking to use laterally aligned packaging machines, as occurs in the L-shaped interconnection.
Ideal for situations in which packages cannot fall, this model directs the packages from the main packaging machine following the L-shaped interconnection pattern. However, the packages from the secondary packaging machine are guided by S-shaped belts, overlapping the main belt in the sync point.
Advantages of the Model S
Check out the advantages that the Model S offers below:
- Efficient integration without package tipping: with the use of a curved plastic conveyor, the layout configuration allows products to be integrated without tipping the packages from the interconnected machine.
- Double vertical fillers: this is the most suitable layout for using double machines, that is, Twin Packaging Machine, as the interconnection does not take up space inside the machines.
Model S attention points
Curved belts can limit the speed of the production line and this interconnection model requires additional care for maintenance and conservation of the plastic modular belt.
Model I: two packaging machines for one baler
Interconnection Model I follows the same premise as Model S, where bags cannot fall over during the journey to the cluster. The difference between the two models lies in the positioning of the packaging machines.
Advantages of Model I
Check out the advantages that Model I offers below:
- Simplified operation: this interconnection of Indumak machines requires simpler and, as a consequence, more economical configurations.
- Space optimization: in factories with a linear layout, the Model I stands out by limiting itself to the width of the baler, offering a compact and effective solution.
Points of attention for Model I
We highlight three points of attention for this model:
- Product supply: alerts to the need to evaluate the product supply in the two packaging machines, now positioned in line, instead of side by side. This change may require adjustments to the supply system to ensure continued efficiency.
- Front wrapper plastic reel change: the front VFFS is positioned on a simple structure that lifts the machine by approximately 300 mm. Therefore, changing the reel at the rear of the machine requires the presence of two people, also considering the passage of the package conveyor of the rear machine.
- Demand for depth in the factory layout: Although the Model I saves lateral space (width), it is important to note that this layout occupies more depth in the factory space.
Adaptive customization to the customer’s layout: Indumak’s difference
Indumak understands that each client has unique needs and spaces. Therefore, customizing the interconnection of Indumak machines is essential, so that the installations can be adapted according to the specific layout of each factory.
This flexibility not only optimizes the use of available space, but also allows you to adjust the production process to meet the specific demands of each customer.
More agility for the production process
Regardless of the model chosen, the interconnection of Indumak machines aims to speed up the production process, providing greater production per square meter. Choosing the appropriate arrangement of machines can result in operational efficiency and resource savings.
Customization according to the customer’s layout, combined with the support of our experts, is crucial to guarantee efficiency and success in the implementation of new production lines.
Get in touch with our team of experts and consult the best model for your business!