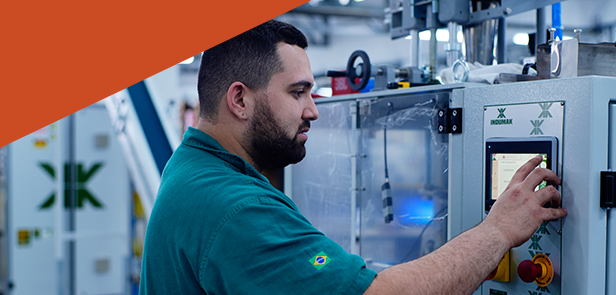
Categoria: Maintenance and Operation
How to ensure the best use of a technical visit in your factory
To lead the packaging automation market, Indumak has always invested in quality, technology and offering a complete and tailored service for each segment and need.
One of the differentials offered by Indumak for your company is the technical visit, which takes place whenever it is necessary to prepare a new project, install the equipment or carry out the maintenance of any machine.
Although this step is carried out by specialists trained to provide excellent service, the host company can collaborate with the success of the visitation with some simple tips that guarantee the best use of a technical visit. Do you want to know what are they? Read on!
Tips for making the most of a technical visit
Whether for installation or maintenance, get organized to make the most of the presence of the Indumak professional in your industry for a productive, informative and effective visit.
In the case of a project preparation visit or the long-awaited installation, try to have all the necessary information at hand. The more information the technician has, the more certain your service will be, meeting your needs and saving you time and money.
Check out some points that should be observed before installing the equipment and informed to the technician at the time of the visit:
- Is your dock prepared to receive equipment of this size?
- What will the unloading process be like?
- How will the equipment be handled up to the installation site?
- Is the route free and safe?
- Does the company have the necessary material to test the equipment before putting it into full operation?
- Is the feeding system (elevator, hopper) already installed?
- Is the plastic coil (film) available at your company?
- Is there a pneumatic point dimensioned 1 meter from the installation site of the equipment?
- Is the pneumatic network free of contaminants in the compressed air (according to ISO 8573)?
- Is there an electrical point dimensioned at 1 meter from the installation site of the equipment?
- Is there a grounding point near the equipment with a maximum resistance of 5 ohm?
In the case of installation of new equipment, the presence of a maintenance technician from your company is mandatory to monitor the implementation, as well as to train the use of the new machinery.
Technical visit for maintenance
If you already have the equipment installed and have requested the visit of an authorized Indumak technician to perform maintenance, make a list of your doubts and your goals. On the day of visit, leave the equipment prepared according to the requests received at the time of scheduling, as space and facilities available.
When receiving the technician, briefly explain how the factory works and what are the safety measures adopted. Allow machine operators to talk to the technician to take advantage of the specialist’s presence and ask all necessary questions.
Thus, you will ensure the best use of a technical visit, and everyone will feel more comfortable sharing information and experiences from day to day, resulting in a much more effective job.
After the visit, leave your impressions in the comments on the service report or directly at Indumak Customer Service, either to express your satisfaction or to suggest improvements. This is the best way to measure the service performance of our internal and external teams.
In the urgency of any support, Indumak also offers PRATI (Indumak Technical Service), which can be done remotely by e-mail, by message or by phone. In this case, it is even more important that you have all the information and questions at hand to help you with whatever you need.
Our support team is in daily contact with customers from all over the world to facilitate and improve the performance of the machines and the productive results of the industries. Count on us when and where you need it!