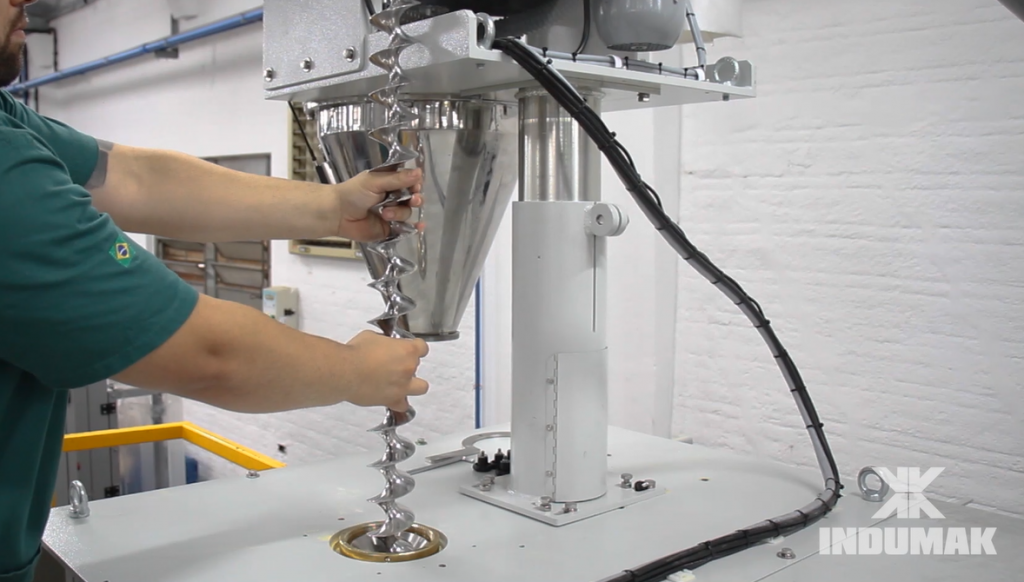
Categoria: Manutenção e Operação
Entenda o que é matriz de criticidade de equipamentos e como definir essas manutenções
Você sabe quais são as necessidades de manutenção dos equipamentos do seu parque fabril e o grau de vulnerabilidade de cada um deles?
Essas são informações importantes para evitar paradas não programadas, prejuízos com a interrupção da produção e até mesmo os custos altos que podem envolver um conserto inesperado.
E é na matriz de criticidade dos equipamentos que todos esses dados são reunidos. Com ela em mãos, fica mais simples e prático elaborar um plano de manutenção preventiva forte, que permitirá que você tome decisões rapidamente sobre as ações preventivas da sua indústria.
Agora que você já sabe para o que serve a matriz de criticidade de equipamentos, vamos entender como ela funciona?
Leia também: Entenda os tipos e a importância da manutenção industrial
O que é a matriz de criticidade do equipamento?
A avaliação da criticidade atribui uma classificação a cada tipo de equipamento do chão de fábrica. Essa identificação inclui:
- Vulnerabilidade (probabilidade de falha)
- Criticidade (consequência da falha)
É essa classificação, dada a uma peça ou equipamento, que vai determinar com que frequência a inspeção deve ser feita.
A matriz de criticidade fornece ao responsável pela manutenção um guia sobre quais notificações e ordens de serviço podem ser reprogramadas para uma data futura e quais exigem atenção imediata.
Leia também: 5 dicas para reduzir custos de manutenção industrial
Processo de análise da matriz de criticidade de um equipamento
Embora pareça simples, o processo de análise de criticidade exige um esforço de toda a organização, devido às diferentes informações que ele reúne. Para fazer a avaliação de criticidade através do método ABC, classifique seus equipamentos entre:
- Rotativo: o equipamento pode ser instalado e desmontado de locais funcionais
- Móvel: equipamento de elevação, equipamento de incêndio de emergência, veículos, escadas
- Fixo: pode exigir inspeção – torres, vasos, tambores, trocadores
Depois, atribua uma pontuação a cada uma das máquinas, conforme os critérios:
- Segurança
- Meio Ambiente
- Qualidade
- Produtividade
- Manutenibilidade
- Custos
A cada um destes critérios, atribua um nível de impacto:
A: alto impacto
B: impacto médio
C: baixo impacto
Com esta análise em mãos, utilize o fluxograma de decisão:
Como resultado, suas máquinas serão classificadas da seguinte forma:
- A: equipamento altamente crítico
- B: equipamento moderadamente crítico
- C: equipamentos de baixa criticidade no processo
Leia também: Como garantir o melhor aproveitamento de uma visita técnica em sua fábrica
Os equipamentos críticos foram definidos. E agora, qual o próximo passo?
Uma vez que você tenha definido quais máquinas são as mais críticas, é hora de agir. Uma boa maneira de começar é estruturando um plano de manutenção que envolva as diferentes estratégias de manutenção: corretiva (executar até a falha), preventiva e preditiva.
Máquinas críticas devem ser o foco da manutenção preditiva, pois se destina a identificar possíveis falhas, preferencialmente em um estágio inicial, para evitar mais danos à máquina.
Outros métodos de análise de criticidade
Além deste método ABC, existem outros métodos de avaliação da criticidade das máquinas, como uma matriz GUT, o RCM (Manutenção Centrada em Confiabilidade) e FMEA (Análise de Modo e Efeito de Falha).
Importante: uma vez que cada equipamento é classificado, os gestores de manutenção podem tomar decisões baseadas em risco, em vez de intuição. Assim, todas as atividades e processos relacionados à confiabilidade serão executados com muito mais facilidade.
Agora que você já sabe como otimizar o processo de agendamentos de manutenção dos equipamentos da sua empresa, que tal descobrir os 8 passos para reduzir o tempo de setup na produção? Confira gratuitamente em nosso e-book!