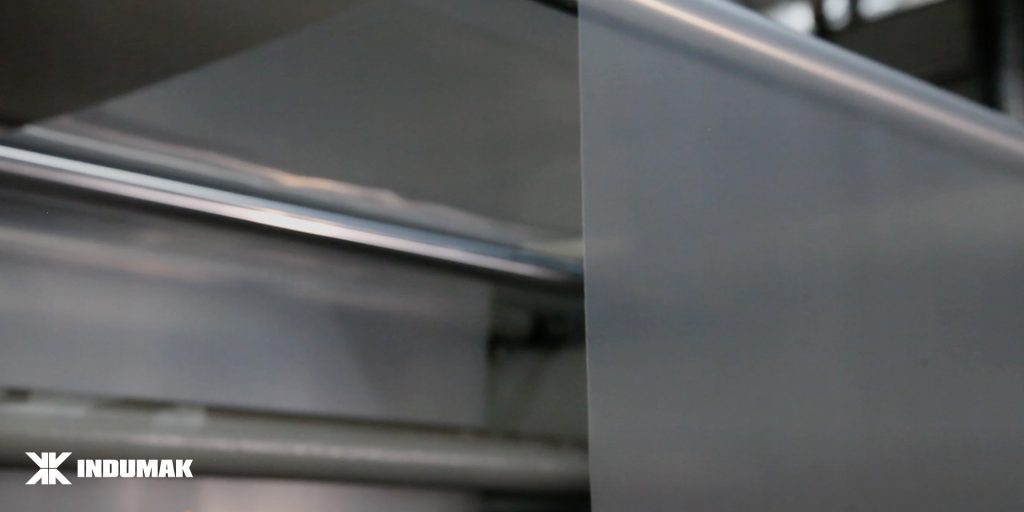
Categoria: Sem categoria
KNOW THE ADVANTAGES OF THE AUTOMATIC ALIGNER FOR PLASTIC FILM
The film misalignment in your vertical filler can cause packaging and product waste, excessive machine downtime, as well as loss of quality of the finished package.
It causes a considerable decrease in the general efficiency that can be measured by the OEE index, the indicator most used by the industry to manage the effectiveness of equipment and production lines.
Understand how the automatic plastic film aligner helps in the process
To avoid this negative scenario, the automatic plastic film aligner is a recommended feature of vertical fillers to ensure that the performance and quality of the final product is achieved.
Below are some possible causes for film misalignment, which the automatic aligner can correct during machine operation. Check out!
Possible causes:
- The film is not centered on the reel axis
- Film is not wound correctly
- The film feed rollers in the machine are not parallel (they are misaligned with each other or with respect to the collar of the pack former)
- The bobbin is not rotating freely (there is some mechanism working hard, due to deregulation)
- The forming tube collar is damaged (may wear out with age and use)
- Bobbin splicing was not performed correctly
- The bobbin brake or motorized unwinder is operating improperly, leaving the bobbin without the necessary tension
How does the automatic plastic film aligner work?
The automatic plastic film aligner is an automation feature of the vertical packaging machine, consisting of two film positioning sensors, which drive a geared motor moving the entire film passing cart.
Once the positioning of these two sensors has been adjusted, the aligner will always keep the overlap centered.
What are the advantages of automatic film aligner?
As the main advantage, we highlight the autonomy of the machine, which ends up eliminating this function from the operator’s routine.
In this case, the machine adjusts itself automatically, and the operator can focus on other activities under his/her responsibility, saving film and improving equipment efficiency.
As it is optional, this set can be used in MG-1000, MG-8000, MG-250 and MG-320 packers, with current designs, or, in cases of upgrade, due to changes in electrical and mechanical components, the application can be done through simulation with Indumak’s after-sales team.
At Indumak, the parts sales department offers, in addition to spare parts, consumables and accessories for packaging, bagging, grouping and product handling lines, with ease and security of purchasing directly from the factory.
Talk to us to request a quote and learn about financing conditions to add more efficiency to the automatic packaging of your product.